Pipeline Mechanical End Couplings
Aditya Steel Engineering Co. is a leading manufacturer and supplier of high-quality Pipeline Mechanical End Couplings. Trust us for innovative solutions ensuring your operations run smoothly and efficiently.
Pipeline Mechanical End Couplings are a type of pipe fitting used to connect two pipes together, providing a secure and leak-tight seal. They are designed to withstand various environmental conditions, including high pressures, temperatures, and corrosive substances.
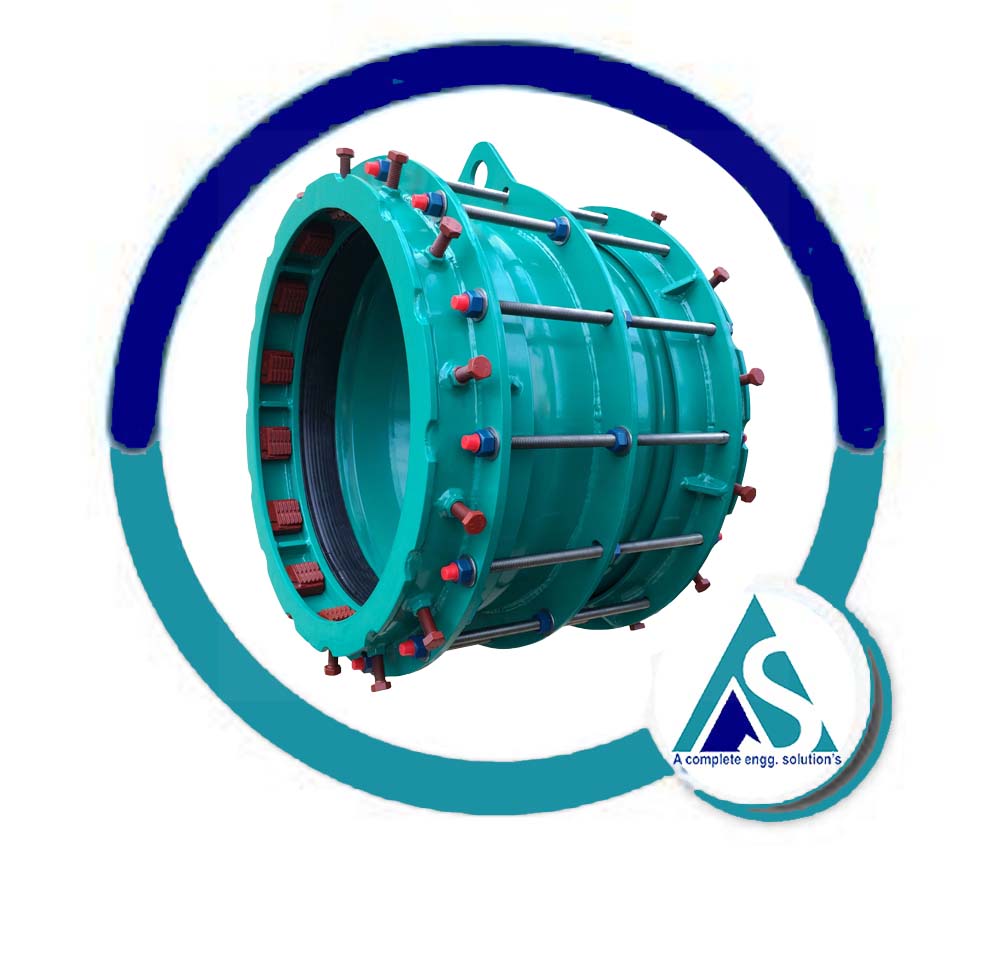
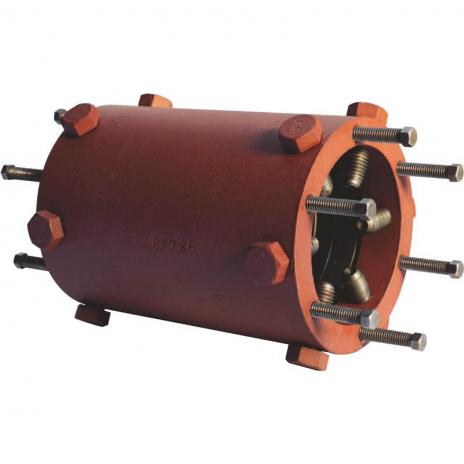
Pipeline Mechanical End Couplings are used to connect two pipes together, providing a secure and leak-tight seal. Here are some key features and benefits:
Key Features:
1. Mechanical end coupling design: Allows for easy installation and removal.
2. Durable materials: Typically made from high-strength materials, such as stainless steel or carbon steel.
3. Sealing elements: Equipped with sealing elements, such as gaskets or O-rings, to ensure a leak-tight seal.
4. Size range: Available in various sizes to accommodate different pipe diameters.
Benefits:
1. Easy installation: Quick and simple to install, reducing labor costs and downtime.
2. Leak-tight seal: Provides a secure and reliable connection, preventing leaks and environmental hazards.
3. High-pressure resistance: Designed to withstand high pressures, making them suitable for various industrial applications.
4. Corrosion resistance: Made from corrosion-resistant materials, ensuring a long service life.
Types of Pipeline Mechanical End Couplings:
1. Standard mechanical end couplings: Suitable for most pipeline applications.
2. High-pressure mechanical end couplings: Designed for high-pressure applications, typically above 1000 psi.
3. Corrosion-resistant mechanical end couplings: Made from corrosion-resistant materials, such as stainless steel or titanium.
Here’s a detailed overview:
Definition: A mechanical end coupling is a type of pipe fitting that connects two pipes together using a mechanical seal.
Purpose: The primary purpose of a mechanical end coupling is to provide a secure and leak-tight connection between two pipes, ensuring the safe and efficient transportation of fluids.
Product Details
Standard Body Materials:
- ASTM A106 Gr. C
- ASTM A105/A350 Gr. LF2
- ASTM A516 Gr. 70
Working Pressure: Variable dependent on size and existing anchored or unanchored piping. Multiple working pressures available upon request.
Seal Materials: Buna-N Packing is standard. Viton, Silicone and other packing available upon request.
Options:
- NACE MR0175/ISO 15156 compliant material
- Marine epoxy paint for corrosion protection
- Anodes for cathodic protection
Key Components:
1. Coupling body: The main component of the mechanical end coupling, which houses the seal and connects to the pipes.
2. Seal: A gasket or O-ring that creates a leak-tight seal between the coupling body and the pipes.
3. Bolts and nuts: Used to secure the coupling body to the pipes.
Types of Mechanical End Couplings:
1. Standard mechanical end couplings: Suitable for most pipeline applications.
2. High-pressure mechanical end couplings: Designed for high-pressure applications, typically above 1000 psi.
3. Corrosion-resistant mechanical end couplings: Made from corrosion-resistant materials, such as stainless steel or titanium.
Advantages:
1. Easy installation: Quick and simple to install, reducing labor costs and downtime.
2. Leak-tight seal: Provides a secure and reliable connection, preventing leaks and environmental hazards.
3. High-pressure resistance: Designed to withstand high pressures, making them suitable for various industrial applications.
4. Corrosion resistance: Made from corrosion-resistant materials, ensuring a long service life.
Applications:
1. Oil and gas industry: Used for pipeline connections in oil and gas applications.
2. Chemical processing: Used for connections in chemical processing plants.
3. Power generation: Used for connections in power generation plants.
4. Water treatment: Used for connections in water treatment plants.
Here are some common materials used for Pipeline Mechanical End Couplings:
1. Carbon Steel: A cost-effective and widely used material for mechanical end couplings.
2. Stainless Steel: Offers excellent corrosion resistance and is often used in applications where corrosion is a concern.
3. Alloy Steel: Provides high strength, toughness, and resistance to corrosion and wear.
4. Duplex Stainless Steel: Offers excellent corrosion resistance, high strength, and good weldability.
5. Super Duplex Stainless Steel: Provides excellent corrosion resistance, high strength, and good weldability.
6. Titanium: Offers excellent corrosion resistance, high strength, and low density.
7. Monel: A nickel-copper alloy that provides excellent corrosion resistance and high strength.
8. Hastelloy: A nickel-chromium-molybdenum alloy that offers excellent corrosion resistance and high strength.
9. Inconel: A nickel-chromium alloy that provides excellent corrosion resistance and high strength.
Coatings:
1. Epoxy Coating: Provides excellent corrosion resistance and is often used in applications where corrosion is a concern.
2. Polyurethane Coating: Offers excellent abrasion resistance and is often used in applications where abrasion is a concern.
3. Zinc Coating: Provides excellent corrosion resistance and is often used in applications where corrosion is a concern.
Here are some key words related to Pipeline Mechanical End Couplings:
1. Mechanical end coupling
2. Pipeline coupling
3. Pipe fitting
4. Pipe connection
5. Coupling body
6. Seal
7. Gasket
8. O-ring
9. Bolts and nuts
10. Pipeline repair
Long-tail keywords:
1. “Mechanical end couplings for oil and gas pipelines”
2. “Pipeline couplings for high-pressure applications”
3. “Pipe fittings for chemical processing plants”
4. “Mechanical end couplings for water treatment plants”
5. “Pipeline repair couplings for damaged pipes”
Manufacturer of pipe end coupling, pipe mechanical end coupling, pipe weld end coupling, pipe end weld joint coupling, bolted pipe end weld coupling, pipe end joint coupling, pipeline connecting end weld couplings.
OUR MAIN MANUFACTURING, FABRICATION AND EXPORT COUNTRIES:
- ASIA – India, Japan, Thailand, Singapore, Sri lanka, Bangladesh, South Korea, Indonesia, Philippines, Vietnam, Kazakhstan, Turkmenistan, China.
- Middle East – Kuwait, Dubai, Saudi Arabia, Qatar, Oman, Bahrain, Jordan, Turkey, Iraq, Yemen, Azerbaijan, United Arab Emirates.
- Western Europe – Germany, France, Netherlands, Belgium, Austria, Switzerland, Luxembourg, Monaco, Liechtenstein
- Eastern Europe – Russia, Ukraine, Poland, Romania, Czechia, Hungary, Belarus, Bulgaria, Slovakia, Moldova.
- Northern Europe – United Kingdom, Sweden, Denmark, Finland, Norway, Ireland, Lithuania, Latvia, Estonia, Iceland, Isle of Man, Faeroe Islands
- Southern Europe – Italy, Spain, Greece, Portugal, Serbia, Croatia, Bosnia and Herzegovina, Albania, North Macedonia, Slovenia, Montenegro, Malta, Andorra, Gibraltar, San Marino, Holy See
- South America – Argentina, Chile, Brazil, Colombia, Paraguay.
- Western Africa – Nigeria, Ghana, Côte dIvoire, Niger, Burkina Faso, Mali, Senegal, Guinea, Benin, Togo, Sierra Leone, Liberia, Mauritania, Gambia, Guinea-Bissau, Cabo Verde, Saint Helena
- Northern Africa – Egypt, Sudan, Algeria, Morocco, Tunisia, Libya, Western Sahara.
- Southern Africa – South Africa, Namibia, Botswana, Lesotho, Swaziland
- Eastern Africa – Ethiopia, Tanzania, Kenya, Uganda,Mozambique, Madagascar, Malawi, Zambia, Zimbabwe, South Sudan, Rwanda, Burundi, Somalia, Eritrea, Mauritius, Djibouti, Réunion, Comoros, Mayotte, Seychelles